The Importance of Measuring Efficiency and Production Ratios in an Auto Repair Shop
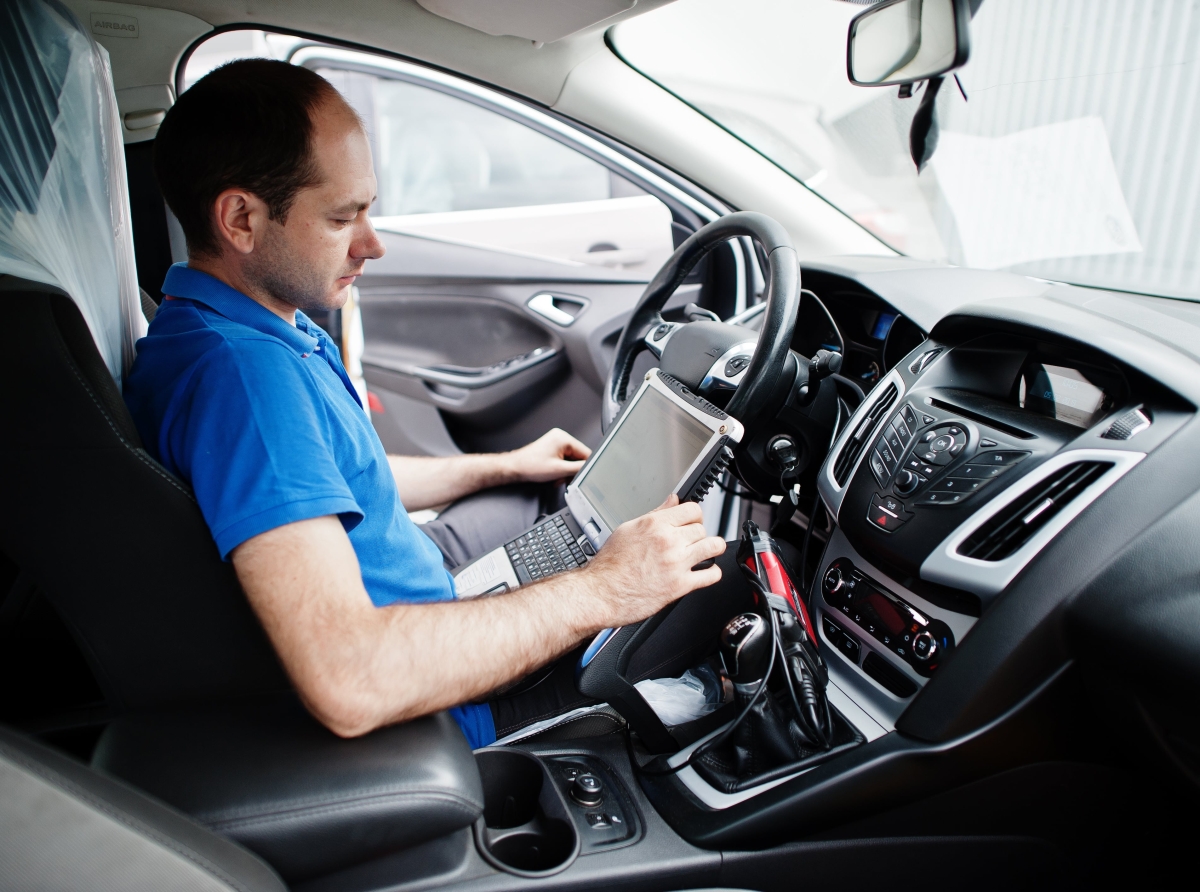
The profitability of an auto repair shop does not rely solely on mechanics' skills or customer satisfaction but also on optimized resource management and precise performance tracking. Measuring efficiency and production ratios helps to understand how the business operates and identify areas for improvement. Here's why and how.
Understanding Efficiency and Production
Before diving into measurements and ratios, it’s important to clarify two fundamental concepts: efficiency and production.
- Efficiency : Refers to the quality of work completed with minimal resources. In an auto repair shop, this means performing high-quality repairs on the first attempt, reducing returns or errors. Efficiency leads to increased customer satisfaction and minimizes the waste in time and materials.
- Production : Measures the amount of work completed over a given period, such as billable hours or the number of repairs performed. High production ensures a steady revenue stream.
These two concepts are complementary. A shop can be highly productive but inefficient if poor repairs lead to returns. Conversely, a highly efficient but low-production shop may not generate enough revenue to cover fixed costs.
Why Is Measurement Crucial?
In any workplace, what isn’t measured cannot be improved. This principle is especially relevant in an auto repair shop, where costs are high, and margins can be slim. Here’s why measurement is essential:
- Identify Weak Points : By tracking precise indicators, shop owners can pinpoint bottlenecks, such as downtime between repairs, delays in receiving parts, or underperforming technicians.
- Monitor Overall and Individual Performance : Ratios evaluate not only the shop's overall performance but also the productivity of individual technicians. For instance, you can measure the percentage of billable hours versus hours worked for each employee.
- Optimize Profitability : Understanding the actual costs of each repair, including labor and consumed resources, makes it possible to set fairer prices and eliminate unnecessary expenses.
- Enhance Customer Satisfaction : Regular measurements ensure that repairs are completed on time and with impeccable quality, reducing returns and complaints.
- Anticipate and Plan : Trend analysis allows shops to predict busy periods, adjust staffing levels accordingly, or invest in equipment to boost performance.
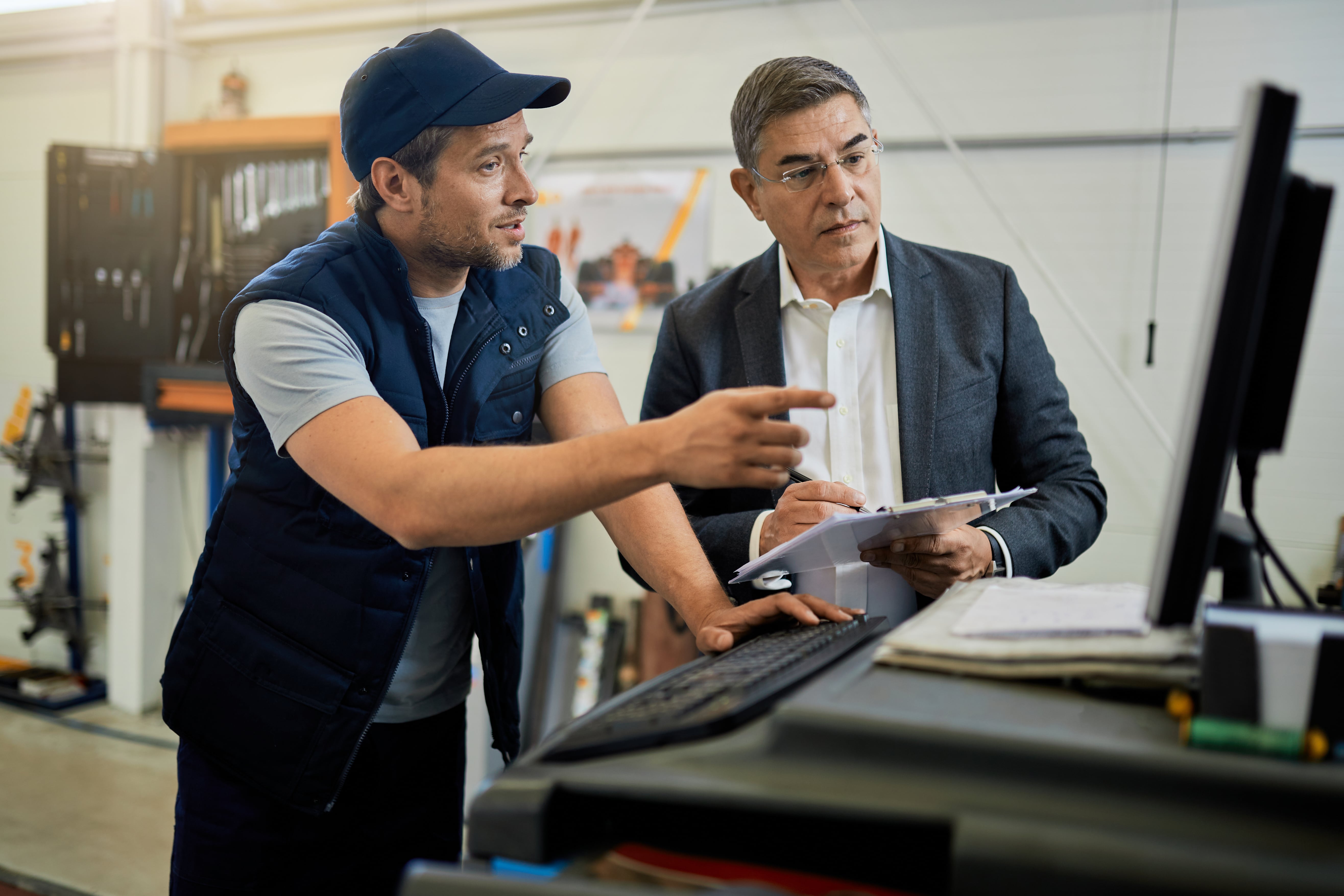
Key Ratios to Measure in an Auto Repair Shop
Here are the most important ratios to evaluate efficiency and production :
- Technician Utilization Rate
This ratio measures the percentage of billable hours compared to hours worked.- Formula : (Billable Hours / Hours Worked) × 100
- Objective : Maximize the time technicians spend on revenue-generating tasks.
- Technician Efficiency
This ratio compares the estimated time for a task to the actual time taken to complete it.
- Formula : (Estimated Time / Actual Time) × 100
- Objective : Determine whether technicians are meeting standard repair times.
- Taux de retour
This ratio evaluates the percentage of repairs requiring adjustments or returns.
- Formula : (Number of Returns / Total Repairs) × 100
- Objective : Keep this rate as low as possible to avoid additional costs and dissatisfied customers.
- Average Repair Time
This ratio measures the average time taken to complete a repair.
- Formula : (Total Hours Worked / Number of Repairs)
- Objective : Identify time-consuming processes and find ways to speed them up.
- Occupancy Rate
This ratio calculates the percentage of time the shop is actively engaged in repairs.
- Formula : (Scheduled Repair Hours / Available Hours) × 100
- Objective : Optimize scheduling to minimize idle time.
How to Measure Effectively
Measuring these ratios doesn’t always require complex tools, but using workshop management software like GEM-CAR is highly recommended for automating tracking and centralizing data. Such tools enable :
- Real-time performance monitoring.
- Automated reporting for quick analysis.
- Forecasting needs based on historical data.
Beyond software, involving technicians in the process is critical. Explaining the importance of these measurements can motivate them to enhance their performance.
Benefits of a Measurement-Driven Management Approach
Integrating regular measurements and analyzing ratios offers substantial advantages :
- Continuous Improvement
Data allows for process adjustments and targeted technician training to boost efficiency.
- Cost Reduction
Identifying waste sources, such as lost time or unused parts, helps eliminate them.
- Revenue Growth
Higher productivity and efficiency result in increased work volume and satisfied customers.
- Informed Strategic Decisions
Measurements support fact-based decisions, such as hiring new technicians, investing in tools, or revising pricing structures.
Conclusion
Measuring efficiency and production ratios in an auto repair shop is an essential practice for any owner seeking to enhance profitability and service quality. These metrics provide valuable insights into shop performance, highlight areas for improvement, and ensure optimal management. Ultimately, a shop that measures, analyzes, and acts on its data is better equipped to tackle market challenges and achieve sustainable growth.